Becket Blower Wire Guide
Yanmar marine industrial diesel engine ha l series service repair manual download yanmar 2tnv70 operation manual pdf download view and download yanmar 2tnv70. Instant download models 4hal industrial engine 6hal industrial engine 6hal t industrial engin 6hae marine engine 6ha hte marine engine this is the most complete service repair manual for yanmar marine industrial diesel engine hal series. Yanmar ha hal series marine diesel engine workshop service repair manual download this is the most practical service repair manual for the original factory yanmar marine diesel engine ha hal series workshop service repair manual download ever compiled by mankind. Yanmar marine industrial diesel engine hal series service repair manual download. This is the most complete service repair manual for yanmar marine industrial diesel engine hal series this manual contains service repair procedures assembling disassembling and everything you need to know.
Cause 1 – The cad cell (flame detector) is seeing light Action:. Turn the power off to the burner. Loosen control.
Verify there are not any exposed wires. Remove yellow cad cell wires from the back of the GeniSys Primary Control. Turn the power back on. The flame light should go out on the Primary Control Additional Action: If the light remains on:.
Verify the cad cell is not seeing any apparent light. If the flame light remains on, replace the GeniSys Primary Control. If the light goes off, replace the cad cell (part number 7006U).
Notes: See the for more information. Cause 1 – The GeniSys Primary Control is in a hard lockout Action: The Genisys Primary Control is in a Restricted (hard) lockout This means the control has locked out 3 times. Additional Actions: Hold the reset button down for 15 seconds. When the reset light goes out, release the button. The control will reset. For more in-depth GeniSys troubleshooting, visit the Notes: The pump prime light will turn on solid once the button is held for 15 seconds until the button is released. Refer to your for more information.
To help troubleshoot the GeniSys control more effectively, use our. Cause 1 – High CO Recommended CO is less than 50 PPM, and usually 10 PPM or less.
If greater, possible causes are:. Excess air. Improper CO2 as recommended by the appliance manufacturer.
Check the appliance manual for recommended CO2. Heat exchanger leaks. Insufficient combustion air supply Action: Check and correct:. Blocked flue, heat exchanger and chimney.
Burner head and nozzle combination. Insertion depth in short furnaces. Flame impingement on damaged refractory. High draft (pulling partially burned products from the base of the flame). Cold furnace. Greatly oversized furnace.
Notes: Refer to our to see start up settings. Cause 1 – Issues with the Blower Wheel or Housing Action:. Check that the blower wheel is tight on the motor shaft.
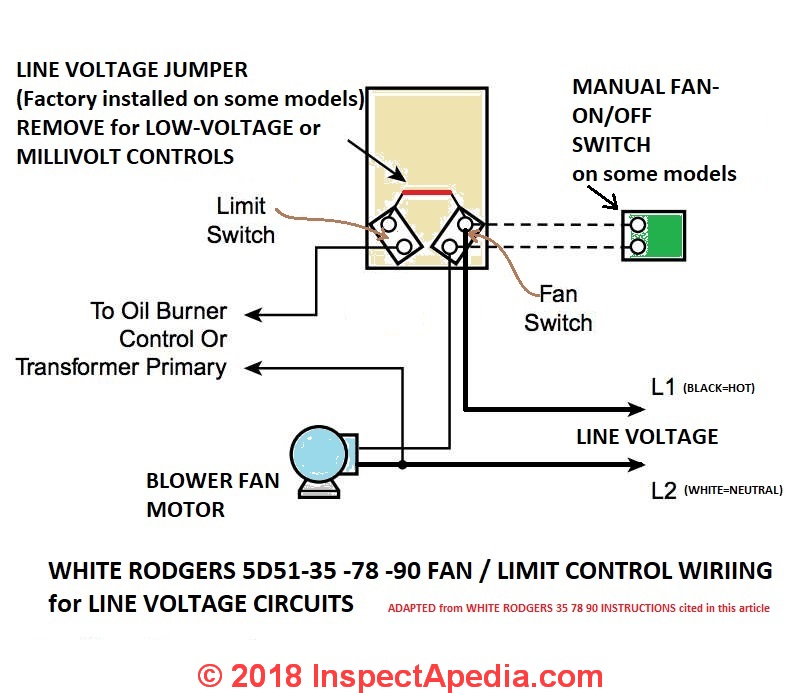
Check for warpage or damage to blower wheel. Make sure the motor is seated properly on the housing. Make sure motor bolts are evenly tightened. Check for debris in burner housing. Check the fit of the motor to housing and for potential damage to the housing. Check shaft alignment.
Make sure the coupling is not too tight. Notes: Refer to the for the proper gap of the blower to motor flange surface. Cause 2 – No power to blower motor Action 1 – CG10 Burner Models: When the limit string is complete, 120v is sent from terminal 5 of the controller subbase to the blower motor. Verify that voltage is present. If voltage is present:.
Verify wiring to the motor is correct. Make sure the motor spins freely. The CG10 replacement part number is 21341U. Action 2 – CG15, CG25 and CG50 Burner Models: When the limit string is complete, 120v is sent from terminal 5 of the controller subbase to the motor contactor coil.
Verify that voltage is present. If voltage is present:. Verify wiring to the motor contactor is correct. If the motor contactor is operating correctly, make sure the motor spins freely. Refer to the for replacement parts. Additional Action: Is jumper JR3 of RM7897 clipped?
If so, check and correct: power supply to blower motor, control signal to starter or contactor, overload trip. Notes: Is JR3 intact? Burner would not have locked out. Cause 4 – Combustion rumble/pulsation – continuous Action: Check and correct:. Draft is too high (tall stack, inadequate draft controls).
Excess air too high, head setting, gas spud obstruction. Correct blower wheel size.
supply pressure to gas train (high or very low pressure drop across regulator). pressure fluctuations coming to gas train from oversized supply regulator,. pressure fluctuations coming to furnace from flue stack (add a barometric). un-approved boiler application (furnace too small). Cause 2 – O2 – too low at high fire with damper at specified opening Also CO2 – too high with damper at specified opening Action: Specified damper opening is a guideline for start-up; don’t be afraid to change it. Normal O2 at high fire is 3 to 4% (CO2 is 9.5 to 10%).
If less O2 (more CO2), check and correct: adequate air supply to boiler room, boiler furnace pressure, firing rate (preferably by clocking a meter, but also compare to data in burner manual), calibration of analyzer, burner head selection and setting. Cause 3 – O2 – too high at low fire with damper at specified opening Also CO2 – too high with damper at specified opening Action: Specified damper opening is a guideline for start-up, don’t be afraid to change it. Normal O2 at low fire is 4 to 5% (CO2 is 8.9 to 9.5%).
[Washington, D.C.]: [U.S. United states marines.

If more O2 (less CO2), check and correct: stack draft (barometric control is recommended for stacks over 10′ tall), firing rate (preferably by clocking a meter, but also compare to data in burner manual), calibration of analyzer, burner head selection and setting. Cause 5 – O2 (CO2) – changes from one day to the next Action: Changes of about 1% O2 (0.5% CO2) are normal. They are caused by changes in fuel properties (utilities change gas properties in response to available supplies and outdoor temperature), air density changes (barometric pressure, temperature, moisture content), and boiler draft changes (outdoor temperature and wind conditions).
If O2 (CO2) changes exceed 1% look for mechanical problems with fuel pressure regulation, draft control, or the burner’s blower and damper systems. A service log of burner settings and performance is recommended. Cause 2 – Not enough air to make rate (low O2 at high fire) Action: Check and correct: adequate ventilation to support all boiler room equipment, high furnace pressure, burner head setting, full opening of burner air damper, debris obstructing air damper, correct air guide or inlet sleeve, blower wheel not tight on motor shaft, correct blower wheel adjustment, combustion air leakage from burner, scroll extension in place in CG10, correct 3 phase motor rotation, blower wheel damage. Manifold pressure is low.
Cause 1 – The Genisys Primary Control is in a soft lockout Action: Press and hold the reset button for at least one second. This will reset the control. Additional Actions: The Genisys Primary Control may lock out for:. Either an unacceptable flame signal. A flame during purge cycles. Too many recycle attempts. An ideal flame signal is1600 Ohms or less.
For more possible causes, see the tech bulletin. Notes: Refer to your for more information. To help troubleshoot the GeniSys control more effectively, use our. Cause 1 – The Genisys Primary Control is in a hard lockout Action: The Genisys Primary Control is in a Restricted (hard) lockout This means the control has locked out 3 times. Additional Actions: Hold the reset button down for 15 seconds.
When the reset light goes out, release the button. The control will reset. For more possible causes, see the tech bulletin. Notes: The pump prime light will turn on solid once the button is held for 15 seconds until the button is released. Refer to your for more information.
Speaker Wire Guide
To help troubleshoot the GeniSys control more effectively, use our.